Après trois ans de travail sur le projet FASD (Simulation de fabrication ajustée pour zéro défaut), il touche à sa fin. Le projet s’est concentré sur le développement de capteurs spécifiques pour mesurer les propriétés des matériaux et des produits (systèmes d’étanchéité de la carrosserie) pendant le processus de fabrication, la collecte de données et le développement de modèles de simulation pour la prédiction ultérieure en temps réel des propriétés du produit et des variables du processus.
Le développement des capteurs et leur intégration avec les capteurs existants, en combinaison avec les modèles de comportement du processus, permettront de se mettre à jour en permanence les résultats du modèle et, par conséquent, lors de la surveillance de la chaîne de production, des décisions en temps réel peuvent être prises sur la variation des paramètres du processus et l’ajustement des caractéristiques finales du produit, éviter ou minimiser les écarts, en veillant à ce que les indicateurs principaux restent dans les plages de tolérance admissibles et en permettant aux superviseurs de la ligne de production de les reconfigurer de manière agile pour la fabrication de lots avec des spécifications de conception différentes.
Le projet FASD est aligné sur le concept de l’industrie 4.0 et fondé sur certains des outils numériques proposés par celui-ci, tels que les jumeaux numériques et la simulation, les mégadonnées, les systèmes cyberphysiques et l’infonuagique, entre autres.
Ce projet a été financé par le ministère de l’Industrie, du Commerce et du Tourisme du gouvernement espagnol avec des fonds FEDER (Fonds européen de développement régional). Nous devons maintenant commencer à exploiter les résultats obtenus.
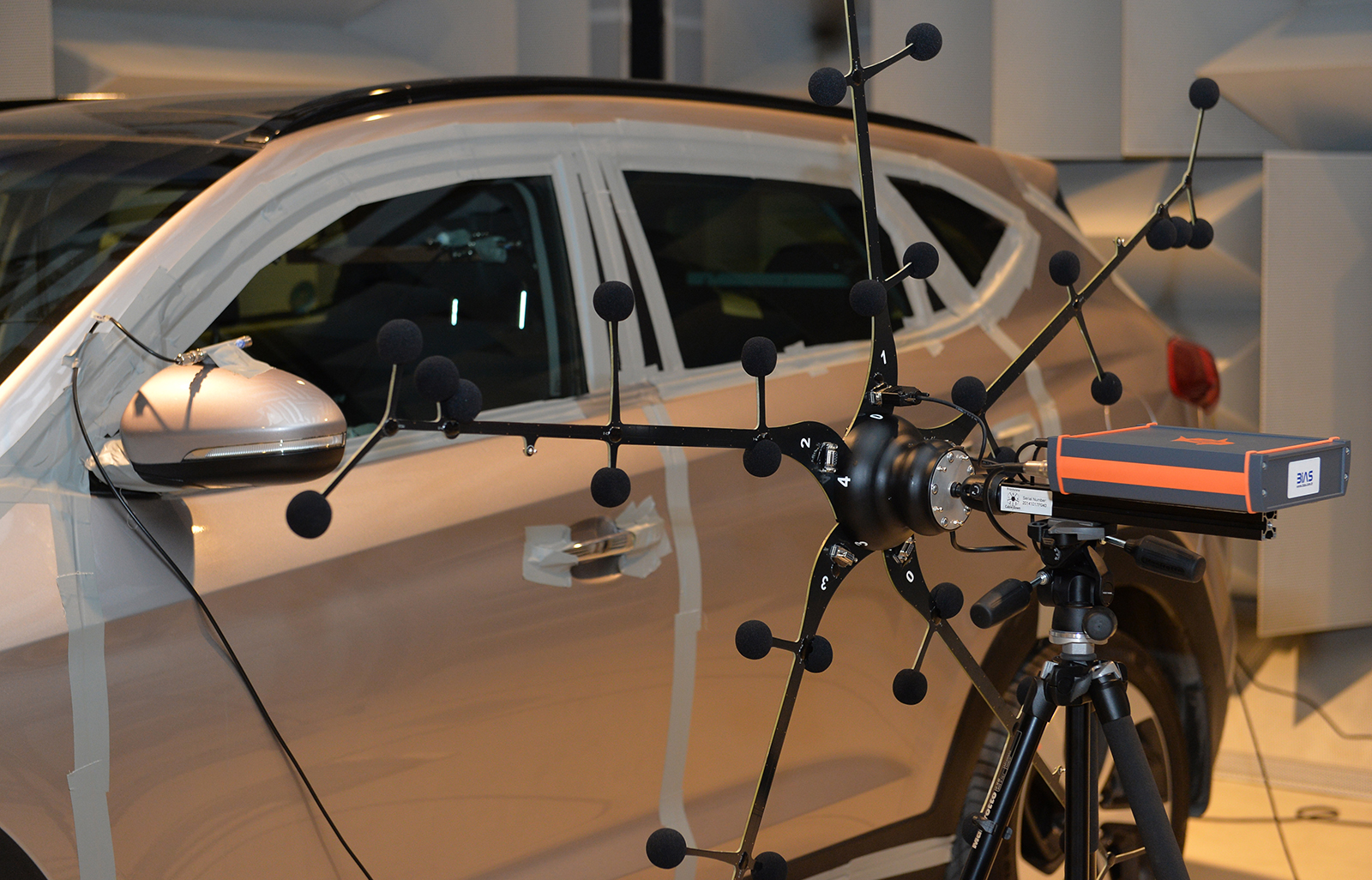